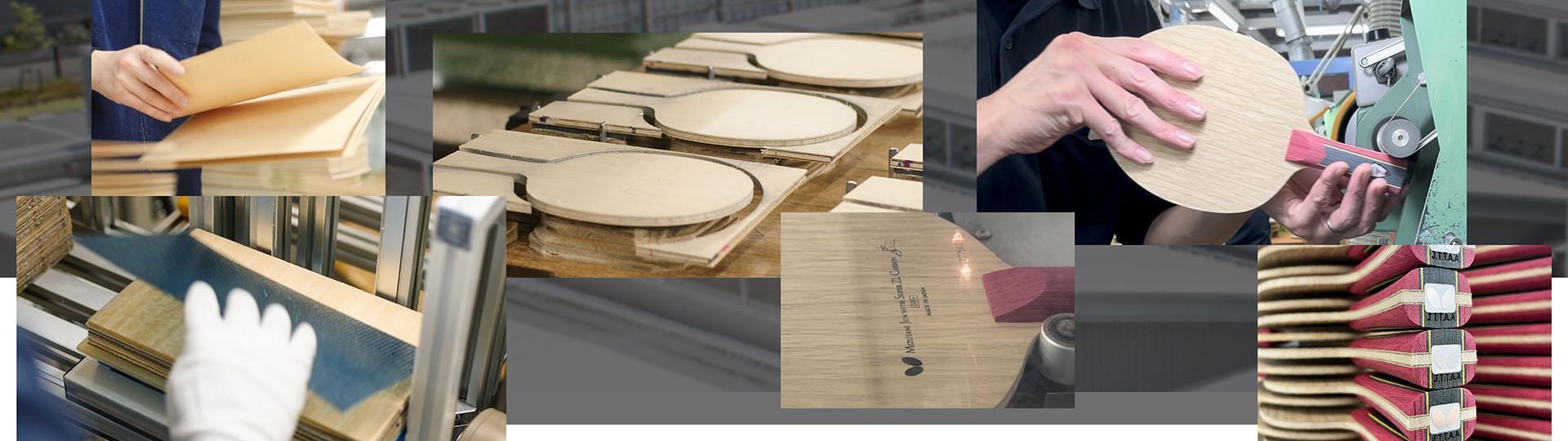
Butterfly TEC, which comprehensively conducts research, development, and manufacturing of Butterfly rubbers and blades, produces blades that are distributed worldwide, including models such as Korbel, Mizutani Jun ZLC, and Timo Boll ALC. There are mainly two types of table tennis blades; shakehand and penhold. Here, we introduce the manufacturing process of shakehand blades, the most commonly used type. It should be noted that blades are primarily made of wood, and their construction patterns can be broadly classified into three types: all-wood multi-ply blades, artificial fiber blades, and all-wood one-ply blades.
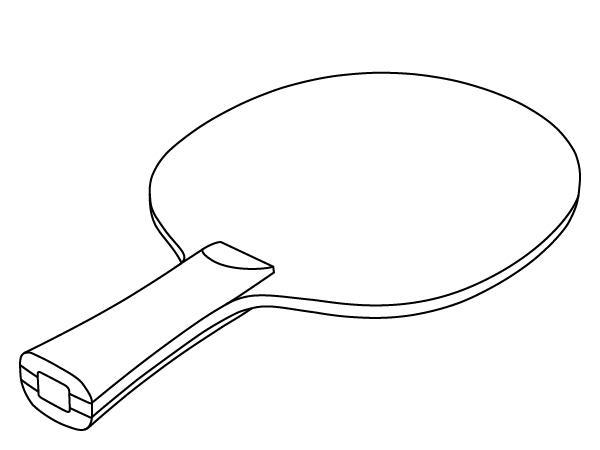
Shakehand
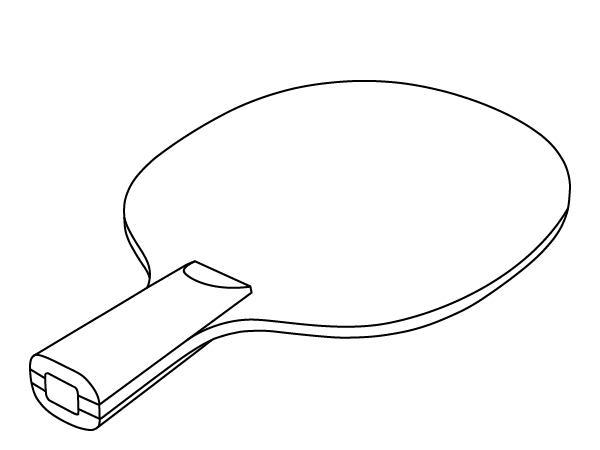
Chinese Penholder
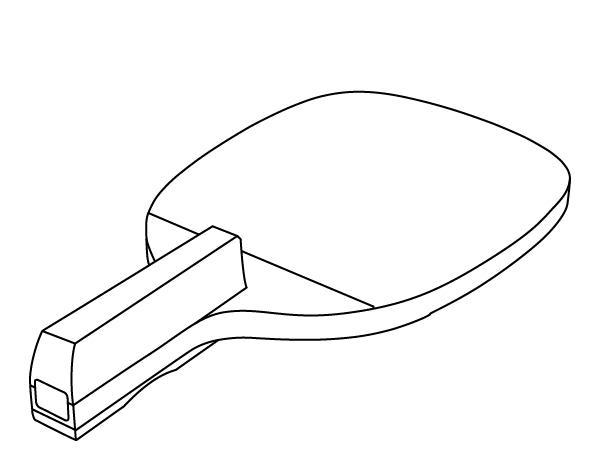
Japanese Penholder
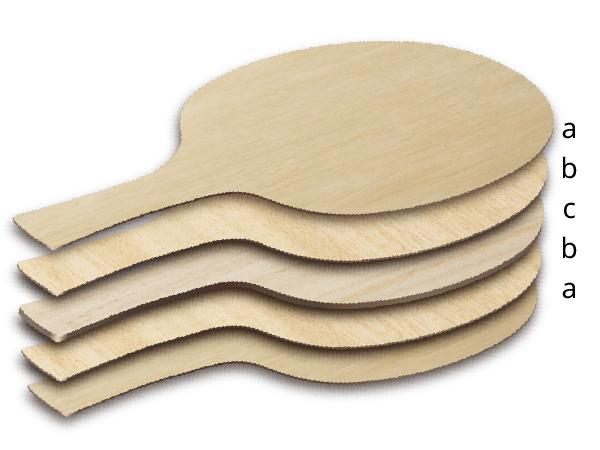
All-wood multi-ply blade
a. Surface wood b. Second layer c. Wooden core
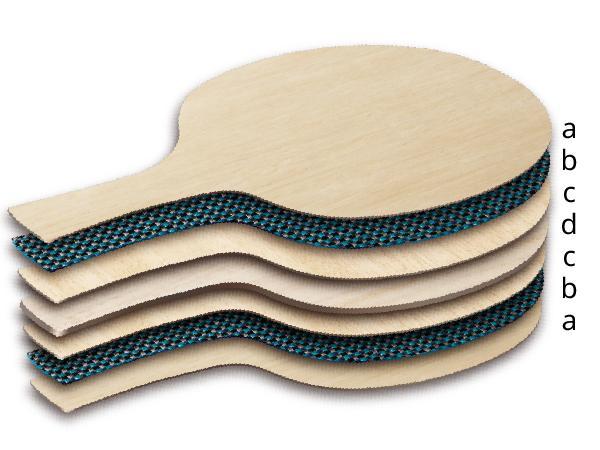
Artificial fiber blade
a. Surface wood b. Artificial fiber c. Second layer d. Wooden core
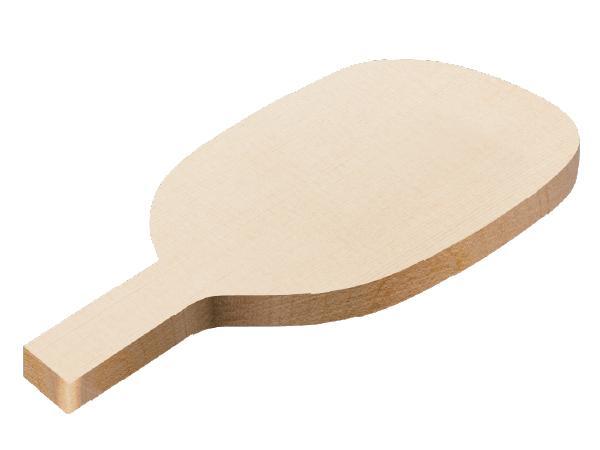
All-wood one-ply blade
Manufacturing Process of blades
We will introduce the main steps in the manufacturing of Butterfly blades. In fact, there are many more processes and quality inspections involved in the meticulous production of blades. Let's take a look at some key stages of the manufacturing process.
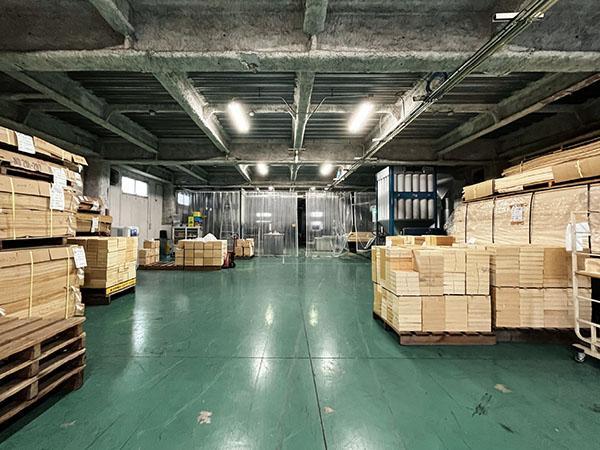
1. Wood Storage
Purchase and store high-quality wood suitable for table tennis blades.
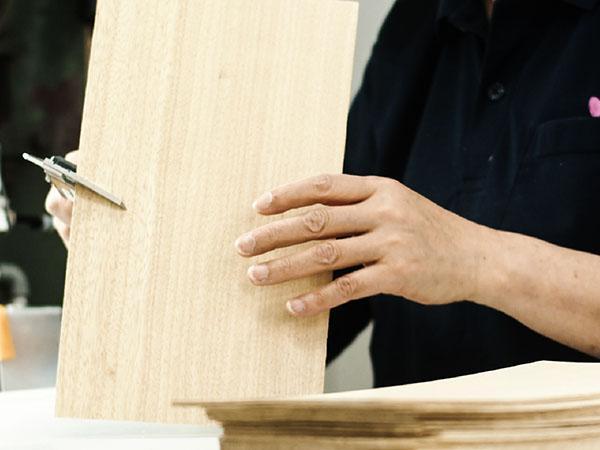
2. Processing the surface wood, the second layer, and the wooden core
Cut and sort the incoming wood, and classify it into detailed ranks. Wood is classified according to its intended use.
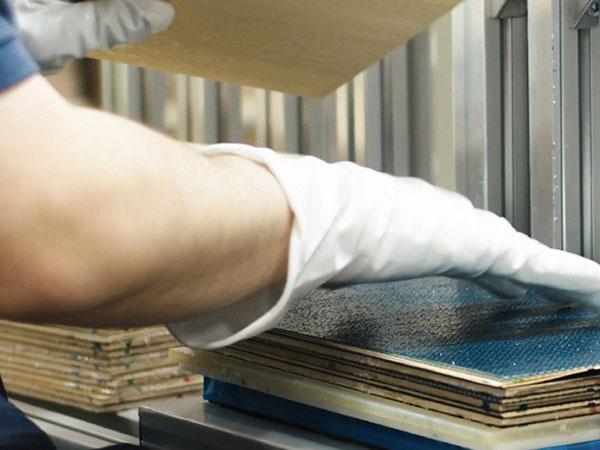
3. Material Bonding
Depending on the plywood structure, wood and special materials are glued together, usually into the size of an A4 sheet.
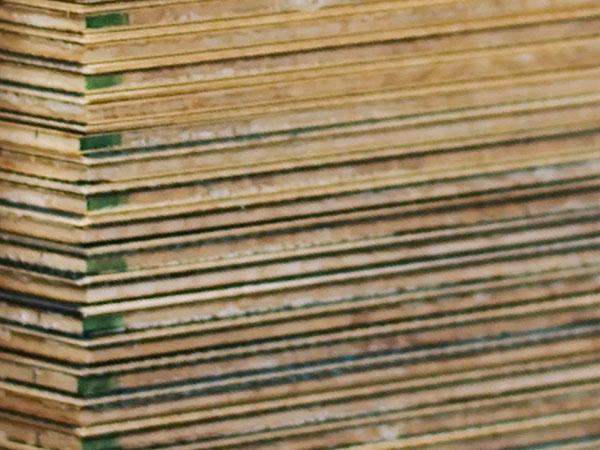
4. Quality Check of Plywood
After letting the plywood sit for a day, check its condition before proceeding with further processing.
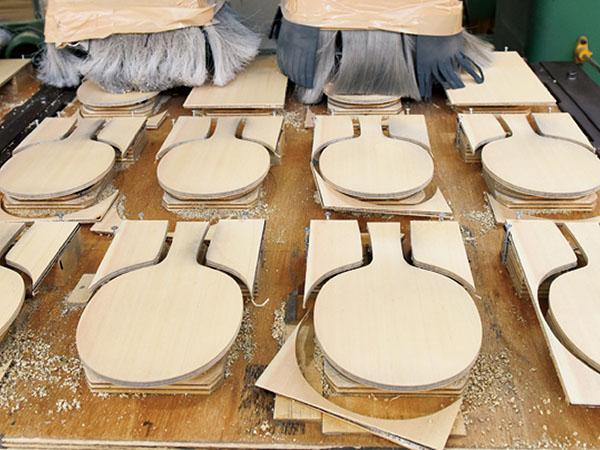
5. Shape Processing #1
The plywood is cut into the shape of the blade by a machine that can accurately cut 24 sheets of plywood into the same shape at once.
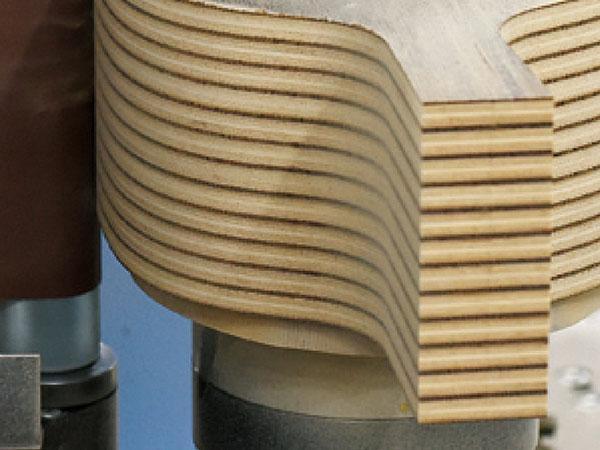
6. Shape Processing #2
The plate (the shape from the previous process) is further processed to a more precise shape with more consistent quality.
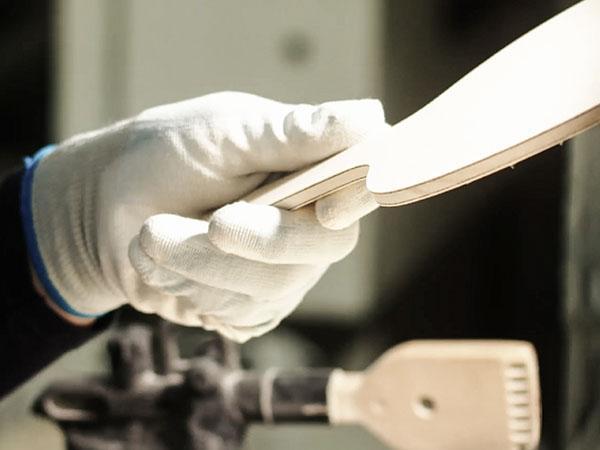
7. Sanding Finishing
The thickness is controlled with very high precision using a sanding finishing machine. Additionally, a protective coating is applied to the surface to complete the plate.
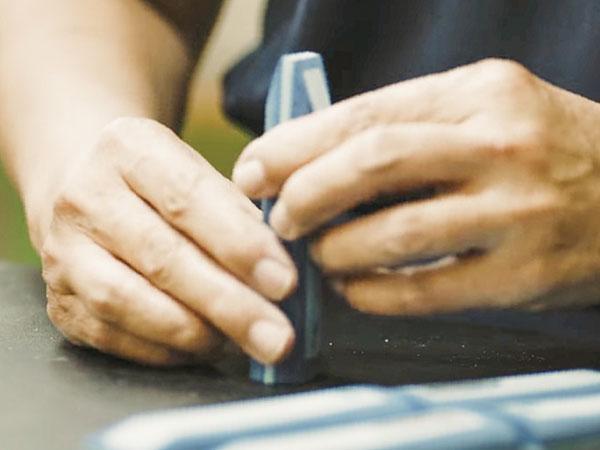
8. Handle Finishing
After quality checking, the handle undergoes processes such as lens attachment.
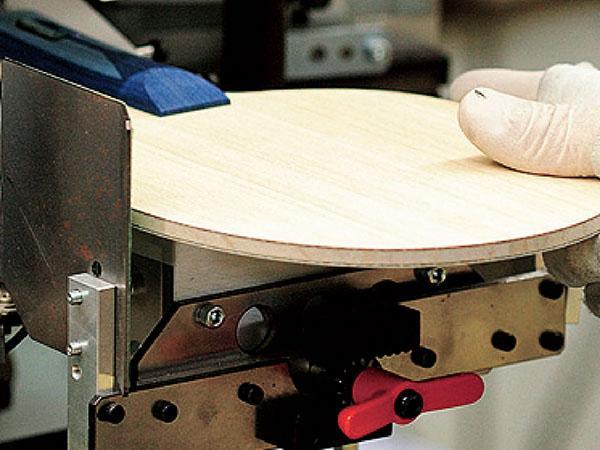
9. Handle Bonding
Flatten the surface of the handle and bond it to the plate.
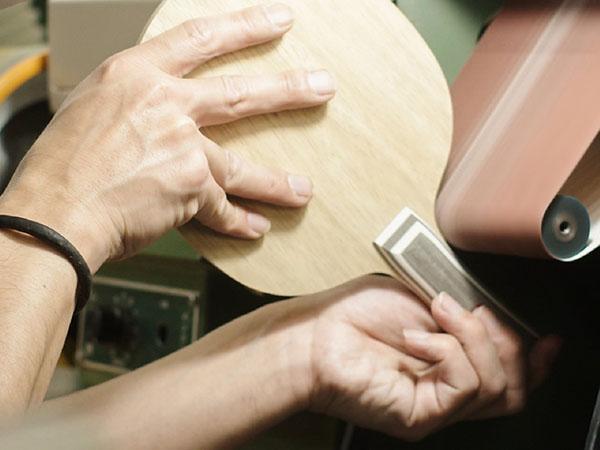
10. Handle Side Finishing
Chamfer the sides and end of the handle (manually performed one by one)
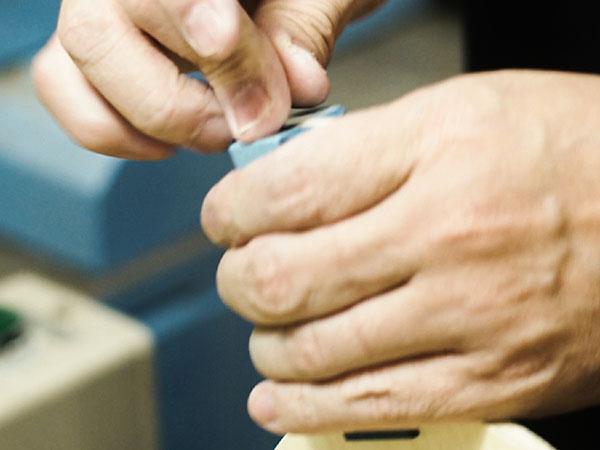
11. Blade Finishing
The blade is finished by hand, undergoing quality checks. The J.T.T.A.A brand is burned into the handle's end, and the logo is attached.
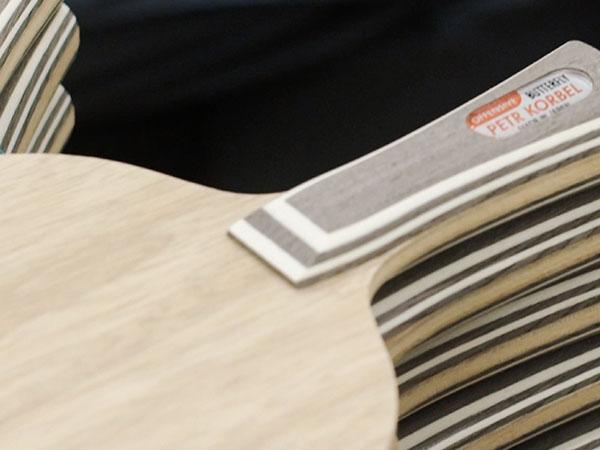
12. Blade Pre-Printing
Blades waiting for blade surface printing are neatly stacked after quality checks.
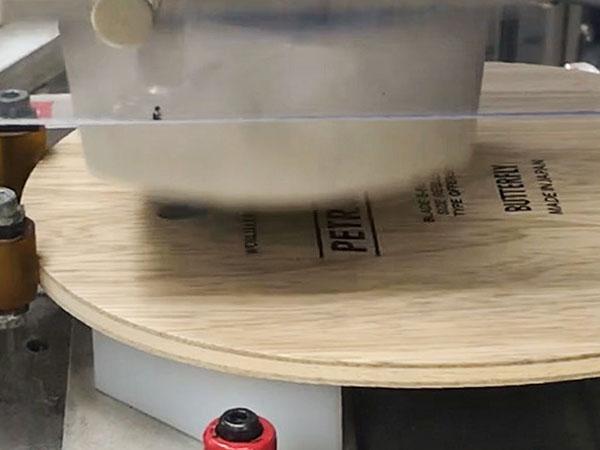
13. Blade Surface Printing
Product names, the Butterfly logo, etc., are printed using a pad printing machine.
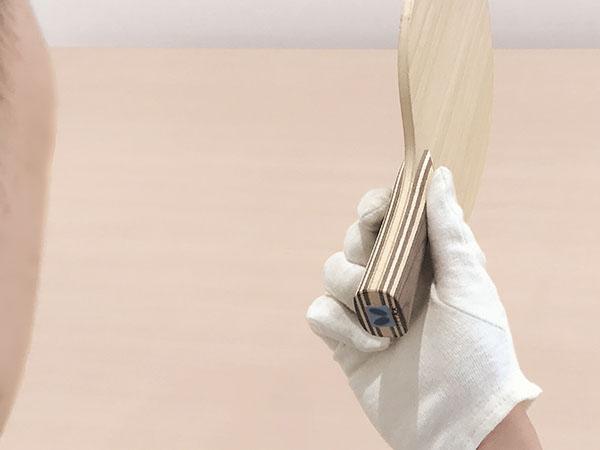
14. Final Inspection
A final inspection is conducted before engraving the serial number (manufacturing number).
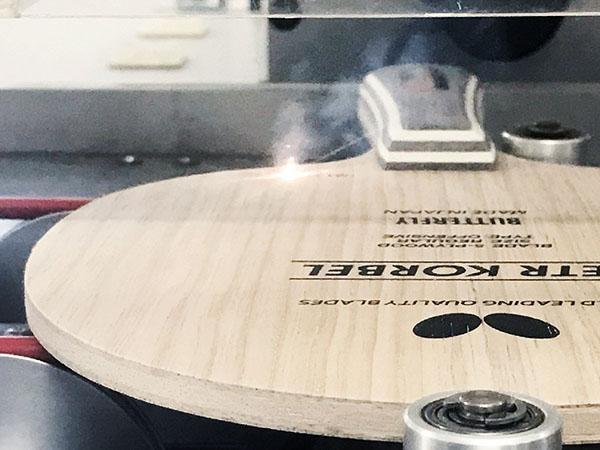
15. Serial Number Engraving
A serial number is engraved with laser, completing a single blade.
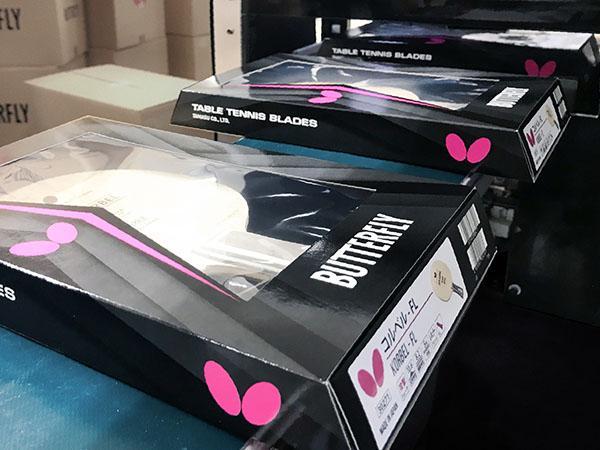
16. Barcode Printing
The box for the blade is printed with a barcode, under which the same serial number as the blade is printed.
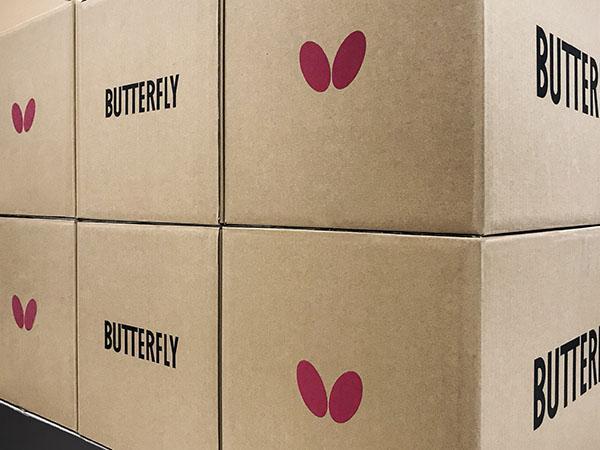
17. Boxing
The blades are boxed up and ready for shipment to all over the world.
Promotion Video
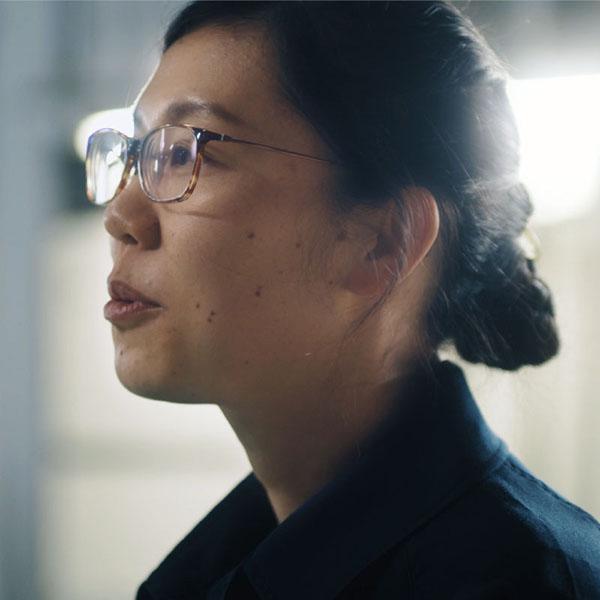
Natsuko Otake
Blade Production Department
If the bounce or touch of a product is not constant, it would be fatal for elite players who live in a world of extreme competition, it might also prevent players who are still trying to obtain new skills from improving. That is why our staff members dedicate themselves every day to manufacturing so that we can provide the same quality in every single rubber and blade we produce for our customers.
Related Videos
Butterfly Blades
Promotion webistes